Swissport unveiled a new four-story office building at its Brussels cargo facility in 2021, marking a milestone in its significant refurbishment initiative launched in January 2019.
The project includes upgrading 25,000 sqm of warehouse space and introducing a Pharma Center. The office building, dubbed building 704, offers over 5,000 sqm of office space and features a dedicated queuing area to streamline truck traffic. Solar panels and a green roof enhance its environmental performance.
The modern building offers employees and customers stunning airport views. This marks a milestone in the complex's refurbishment, which includes a Pharma Center inaugurated in 2019 and a new Dangerous Goods area in 2020. Refurbishment of the 25,000 sqm warehouse with 47 truck loading bays is currently underway.
The architect, having visited the culture museum in Marseille, desired the sidings to resemble a fence but made of concrete. Inspired by the mesh cladding concept of Marseille Museum, the open structure of the new building has been covered with UHPC web panels as structure fence in black color produced by C-concrete, utilizing Extreme® premixed UHPC of InWhite Solution.
Building envelop of level 2-4 is covered with beige precast concrete made with Aalborg White of Cementir’s Sinai plant, lighting up the whole building with an impression of simple, solid and atmosphere.
C-Concrete produced 34 claustra elements, including cutouts of around 280 millimeters and four full walls. Each UHPC web panel has a dimension of 4.7m x 1.5m x 0.15m with a cross-section thickness is 150 mm. The compressive strength of each panel has reached 120Mpa before adding fibers. C-Concrete incorporated PVA& PP fibers to the UHPC premix powder, and 600 liters UHPC were casted in one batch. These full fences, strategically positioned for check-in areas, accommodate all the necessary electronics.
Challenges in UHPC Production Process
Formwork: Sustainable Solutions for Complex Elements
C-Concrete extensively utilizes wood for molds, but for a specific element like this, it's not straightforward. Initially, XPS insulation was considered, but encountered issues with achieving the smooth finish desired by the architect, and sustainability was a concern since one of C-Concrete's pillars is zero waste. XPS can only be used once, resulting in a significant amount of waste for all 38 elements, requiring a new mold each time, which was impractical. The second option was a steel formwork, but the associated costs were prohibitive despite its reusability. After evaluating various options, C-Concrete reverted to using wood formwork, which aligned with their original approach. Fortunately, within the Cordeel group, there is a wood manufacturing facility, C-wood, that assisted in creating the necessary mold. This approach resulted in the desired outcome. Essentially, while this may appear as a standard plate, it has been reinforced and crafted from wood.
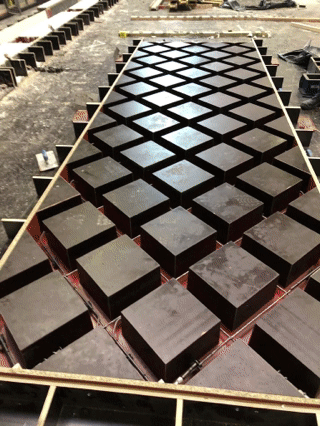
Pigmentation: Overcoming Challenges in Aesthetic Precision and Material Integrity
When incorporating pigmentation, additional water is required as the pigments absorb some of the water used in the concrete mix. Achieving high aesthetic standards demands precise dosing of the color, which is crucial given the varying preferences among architects. Due to the low water-cement ratio C-Concrete works with, instead of adding water, superplasticizer was recommended by Cementir’s expert, sacrificing a bit of strength without significantly affecting the molding and mounting process. Another significant challenge is the potential for lime efflorescence when using black coloration, a concern familiar to pre-casters. To mitigate this, careful storage of the elements is essential. C-Concrete designated a space at the end of their factory, and with supervision from that area, ensured optimal storage until the elements are transported to the construction site.
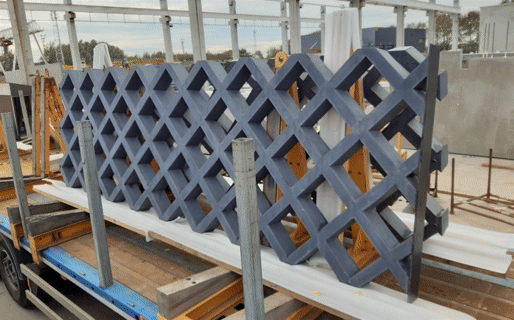
Reinforcement Options: Enhancing Structural Integrity in UHPC Project
Now, onto the type of reinforcements. This marked C-Concrete's inaugural project working with UHPC concrete. Drawing from previous experience with concrete, it was understood that reinforcements could involve fibers or conventional methods, depending on the engineer's calculations. The challenge arose when thin sections of about seven centimeters were encountered; determining the reinforcement method became crucial. While placing the reinforcement is feasible, ensuring its secure positioning is paramount. Initial tests were conducted to ensure proper reinforcement placement, considering C-Concrete's lack of experience with this concrete type. Samples provided by Cementir’s expert were tested in our Lab mixer, revealing the concrete's high viscosity and emphasizing the need to secure the reinforcement to prevent movement. Initially contemplating hybrid reinforcement, the decision was made to opt for PPA fibers or steel fibers, with a preference towards PPA fibers due to their aesthetic nature and the relatively low forces expected on the element. If structural integrity had been a primary concern, steel fibers would have been the preferred choice.
Project Credits:
Project owner: Swissport
Architect: Archipelago and Group Infrabo
UHPC Precaster: C-Concrete
UHPC Premix: Aalborg Extreme (Cementir Group)
White Cement: Aalborg White
Construction: Cordeel Hoeselt NV
Share on